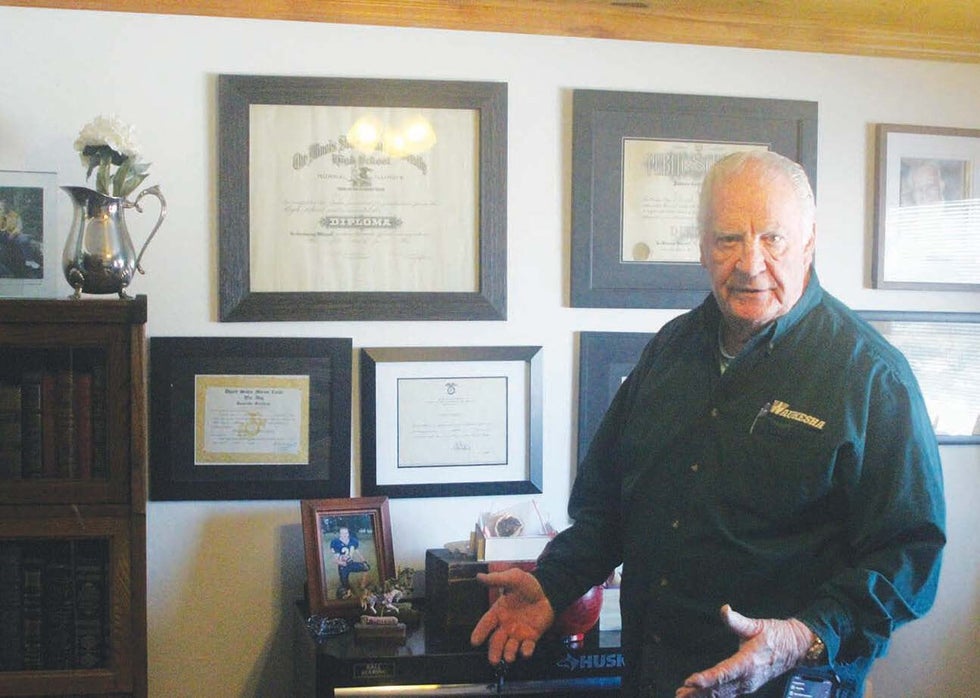
Garrison man recalls WWII dog from youth
By Luke Ulatowski
Garrison resident Lloyd Koehler still honors a World War II veteran he knew in his youth in Illinois: a Doberman pinscher named Major. Beginning in 1942, shortly after the United States entered WWII following the bombing of Pearl Harbor, the U.S. Department of War put out calls for “war dogs” in newspaper advertisements across the country. “They were willing to take pretty much any type of breed of larger dogs,” Koehler said. “They wanted Dober- mans, Huskies, German Shepherds, retrievers - dogs of that size.” In February of 1944, adequate to be trained as messengers, delivering written letters between soldiers who could not
otherwise communicate.
“They would send the dogs with written messages, and the dogs would have to sneak through the enemy lines to get back to the headquarters,” Koehler said. “It is amazing when you stop and think about what they were able to train these dogs to do.”
Major’s crowning moment came in surviving the Battle of Peleliu in September 1944. Peleliu, an island in Japan, held one of the deadliest battles in the Pacific War. An estimat- ed 1,336 U.S. Marines were killed, while the Japanese forces were almost entirely wiped out Lloyd Koehler shows off “war dog” Major’s official certificate of discharge from the military, pictured lower left, dating back to 1945. Photo by Luke Ulatowski back in McNabb, Ill., Koehler’s father, Lloyd Sr., volunteered to put 3-year-old Major to work.
Major was taken to Marine Corps Military Base Camp Lejeune in North Carolina. All dogs the country enlisted were trained as sentry dogs meant to provide human soldiers with warnings of approaching danger. Some dogs, including Major, were found
with an estimated 10,695 casualties. “It was a suicide mis- sion for the Japanese,” Koehler said. “They had decided that they were not going to surrender. To surrender for them was a lack of face, and they would not do that for the emperor.” Major was honorably discharged on June 5, 1945, when Koehler was 2 years old.
“They actually had a parade for him,” Koehler said. “Took him down the street in a parade.” The Putnam County Record reported on Major’s high-profile return, stating he had been “untrained” before his arrival. “When the war ended, they contacted us and said, ‘What do you want to do?’” Koehler said. “‘Do you want the dog back? Because we can’t be assured that he won’t - he’s been trained to kill.’”
After Major’s discharge, his history was never much of a problem for Koehler. Koehler fondly remembers riding around on his back as a three- year-old, and Major never so much as growled. It was shortly after Major’s return that Koehler’s family moved to Oklahoma due to a job change for Lloyd Sr. One of Lloyd Sr.’s cousins lived on a farm outside of McNabb. Seeing that Major enjoyed being out in the country where he could run about, that cousin asked if Major could stay behind, and Lloyd Sr. agreed. Major lived to the age of 10.
Koehler “never thought much about” war dogs when he was younger, but when Lloyd Sr. died, Koehler began research on the topic, and he reached out to the National Archives for Major’s training records, collecting them in a scrapbook he put together for his family. He also framed Major’s discharge certificate.
“Everyone should own a dog,” Koehler said, doting on his current dog, Zoe.
FPE and My Beginning
Well after reading all the Facebook comments, I decided I better chime in. I have a lot to say, so I will have to write a little at a time. If Ted had of still been in charge of NAT at the time, she would have never shut down. My brother-in-law, the late Mike Burns (a winder), told me FPE was hiring and brought me an application to fill out. At that time, I was building Traveling Wave Tubes for the radar systems in the B-58 Hustler. I was hired in 1969 on a Thursday by Rodger B., he told me to start the next day (Friday) and ware safety boots and bring a tape measure. You will be making 4.64 an hour, wow, men have times changed, but that was good money in those times.
My first job was shipping building boxes for radiator fans and accessories. The supervisor at that time I believe was Murphy and he told me we're not building caskets here, just a box, you don’t have to be so precise just nail it together. I guess holding everything within a 1/16 was not a good thing. After about two weeks in shipping, I was moved to the Punch Press, Break and Shear area and worked with Woody. The supervisor there was the late Bernie Lieba, what a guy, he was so funny at times. I can remember the times a bunch of us guys would be hanging on the crane controller box talking and Bernie would come over and say “can I get in on this conversation “, meaning get back on the job, get to work. Bernie had a way with words and people. When he passed, I was heartbroken. Those were great jobs and I learned a lot of things I didn't even know (I came from the electronics industry).
Bernie put me in the radiator leak tank one day to clean it out, nasty job, and i said to myself “he’s testing me’, I cleaned it within 1/16!!!!! After a couple of months in the Punch and Shear area, Bernie asked me if I wanted to learn how to seam the radiator fins and of course I said yes, that was a challenging job.
After a few months of seaming, Bernie asked if I would be interested in learning the Spot Welder and again, I said yes. I was trained on the Spot Welder by Bill Gonzalez and Freddy Bonds. Freddy Bonds, what a guy, he was so much fun to work with. I asked Freddy how he was hired and he told me “I walked in the employees back door one day and Ted was standing by the time clock and asked “can I help you” and I asked if they were hiring and he told me to go to the front desk and tell the lady at the desk (Mary Goble) to hire me and have me start on Monday” yep, that was Ted.
After a few years Bernie put me on swing shaft running the Punch Presses, drill press and Spot Welder. After a year and some months, I went to San Jose City College and got my AA degree in Machine Technology. During my going to school, Bernie asked if wanted to learn the Carlton Radial Drill and man did, I jump for joy and said yes. I kept asking Rodger Bottleson when I could get into the Machine Shop and he told me I would have to finish school.
Working on swing is when I saw just how close Ted was to the employees. One night while running the Radial Drill two Sheriffs came in the back door (office to shop) and Ted was right behind them. Five minutes later they were walking back with a winder in cuffs and Ted asking “How much is the bail, I'll pay it now, I need him here to work” they told Ted “Sir you will have to pay it downtown”. An hour later the winder was back at work. That’s when I realized that plant and the people in it was Ted's life.
We had a lot of management changes just as we had a lot of owners, UV Industries, Exxon, Reliance Electric, Rockwell and Waukesha, I’m sure I missed some. There is so much to say and write about I would have to write a novel. My last day was a Friday in December, there were only three of us left in the plant, myself, Bert Birmingham and I can't remember the last person, all I know we were the last senior employees left, 33, 43 and 46 years.
On my last day I received a phone call from the HR department at Northrop Grumman, they told me they wanted to interview me and wanted to know when I could come in. I told them today is my last day and they asked if I could come on Monday and I said yes. They gave me the machinists test and hired me that Monday pending background check and medical exam. I was told I was highly recommended by NAT and to this day I don't know who recommended me.
So, to make a long story short, I would like to thank everyone for the education, the teachings from shipping, the Iron Shop, Machine Shop, Drafting, Test Department, Tap Gear, Core Stacking, Wood Shop and of course HR. I use all of this knowledge and skills that I have mastered at NAT to this day, engineering, designing and building in my retirement years.
And I would especially like to thank Lloyd Rudy who was my mentor.
Don,
the weave
June 5, 2002 — Waukesha Electric Systems (WES) has announced plans to consolidate power transformer production into plants in Wisconsin and North Carolina, closing its facility in Milpitas, CA, and transferring large power production to its Waukesha, WI, operations.
The Milpitas plant has recently focused on large power transformers used primarily in electric power generation stations. The generation market has been hit hard by recent turmoil within the energy industry, as well as by the influx of imports.
“The market for medium power transformers used in transmission and distribution substations, while soft, remains positive. However, the large power segment, which is closely tied to new power generation construction, is severely depressed and is expected to remain so into the foreseeable future,” said Nancy Dickman, President & CEO for Waukesha Electric Systems. “This makes it impractical for us to continue to operate the Milpitas plant.”
The company said all existing Milpitas plant orders will be produced and shipped before the end of the year as part of an orderly plant consolidation. The majority of the Milpitas plant product offering will then be transferred to the Wisconsin plant, and the company will suspend production of the very large transformer sizes that face the most severe market pressures.
WES will continue to manufacture generator step-up units (GSUs) through 150 MVA and auto-transformers through 300 MVA.
According to Myron Bechtel, Senior Vice President, Transformers & Equipment, “The Milpitas operation, formerly called North American Transformer, was acquired by Waukesha Electric Systems in 1999 from Rockwell International and has been an excellent investment.
“Though the plant itself can no longer be supported based on market conditions, the large power expertise gained through the acquisition will remain within Waukesha Electric Systems and will be utilized to support the transfer of the product offering to the Wisconsin plant.”
Waukesha Electric Systems, Inc., is the largest manufacturer of power transformers in the United States and is a producer of compact modular substations and engineered substation packages. The company has operations in Waukesha, WI; Goldsboro, NC; Milpitas, CA; Canton, OH; and Dallas, TX along with Service Centers in seven states. Markets served include public power, investor owned utilities, merchant power providers, and industrial/commercial firms.
Waukesha Electric Systems is a unit of SPX Corporation, a global provider of technical products and systems, industrial products and services, flow technology and service solutions.
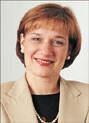
Nacy Dickman
Over the last few years the challenge of change has impacted power systems companies in many ways, but one company, Waukesha Electric Systems, has been particularly effective at mapping out and implementing its growth strategy.
Today, Waukesha Electric Systems (WES) stands out not only as the largest domestic manufacturer of medium-power and large-power transformers (top-rated to 800 MVA), but also as a leading supplier of total energy solutions.
Serving the public power, investor-owned utilities, merchant power providers (GenCo) and industrial/commercial firms, WES has placed a particular emphasis on product quality and reliability and launched a company-wide initiative to optimize the design and manufacture of transformers at each of its plants. WES also provides complete substations that offer innovative solutions in quick turnaround configurations and offers installation, maintenance, parts and training to ensure top performance and maximum value.
"We're proud of the reputation we've built over the years in transformers. But our story doesn't end there," says Nancy M. Dickman, President and Chief Executive Officer of Waukesha Electric Systems, Inc. "These days, our capabilities are unprecedented, allowing us to continue to grow to meet our customer's ever-changing power delivery needs."
The current deregulating energy marketplace has created a real need for experienced suppliers who can deliver total turnkey design, construction and maintenance solutions. "WES is meeting this demand," says Dickman, "through strategic alliances and acquisitions of reliable partners. One example of this is our recent acquisition of Power Systems Development, Inc. PSD is recognized as one of the premier substation design/build firms in the United States and is enhancing Waukesha's capabilities as a provider of complete energy systems solutions, including "Bridge to Grid" generation station packages."
Another way WES is growing to meet customer needs is with its new WES Link(tm) portal on the Internet. WES Link(TM) has two facets: WES View(TM), which offers customers the ability for real-time collaboration with Waukesha engineers on drawings, certified test reports, specifications and other customer-specific documentation; and WES Status(TM), which allows customers immediate access to information concerning the status of their orders at any Waukesha manufacturing location. "WES Link(TM) is designed to enhance our customers' experience," says Dickman. "It is a priority for WES to be a company that customers look forward to doing business with."
The Waukesha Electric Systems story began a little more than 30 years ago, when RTE Corporation (now Cooper Power Systems), a supplier of smaller distribution transformers based in Waukesha, WI, formed a joint venture with ASEA (later ABB) to supply power transformers. Dickman joined the firm in 1990 as General Accounting Supervisor, ascending to Controller, Division Controller and Chief Financial Officer/Vice President of what has grown to become a multi-business, $375 million company today.
In October 1999, she was named General Manager and Vice President of the Waukesha, WI headquarters facility, where she helped spearhead the company's recent $22 million plant expansion. Today, the Waukesha operation encompasses nearly 400,000 square feet of manufacturing, engineering, corporate support and advanced R&D space. WES also has facilities in Milpitas, CA (large-power transformers), Goldsboro, NC (medium-power transformers), Canton, OH (PSD Division for substation design/build/EPC), and Dallas, TX (High Voltage Supply Division, a supplier of re-engineered load tap changers, circuit breaker components, service and training).
WES research and development, based at its Waukesha facility, includes work with the Department of Energy and a consortium of private companies to develop an advanced HTS (high-temperature superconductivity) transformer. Phase I of a comprehensive three-phase program has been completed with the construction of a 1 MVA, single-phase design validation prototype. Phase II, scheduled for completion in 2002, includes further design refinements and the construction and testing of a 5 MVA, three-phase unit that will provide power to the newly expanded WES plant in Waukesha, WI. Phase III will lead to the manufacture and commercialization of a 30 MVA transformer for utility applications. The HTS superconductivity transformer will allow utilities and industry to provide more reliable power to homes and businesses, as demand for electricity increases and the nation's existing systems continue to age.
In October 2001, Dickman was promoted to President & CEO of Waukesha Electric Systems - a role she is uniquely qualified to fill after having demonstrated her solid management skills under three different parent companies for WES - MagneTek, General Signal Corporation, and SPX Corporation (the current parent company).
What does the future hold for WES and its customers? "Each of our 1,400 employees are committed to growth - not just for growth's sake, but to provide our customers with the energy solutions they need," says Dickman. "Through quality products, dedicated service, engineering design and project management know-how, Waukesha Electric Systems continues to explore and develop new and better ways to serve our customers."
NORTH AMERICAN TRANSFORMER IS PURCHASED
North American Transformer in Milpitas, California, is purchased to launch the company into the large power market, name changed to Waukesha Electric Systems.
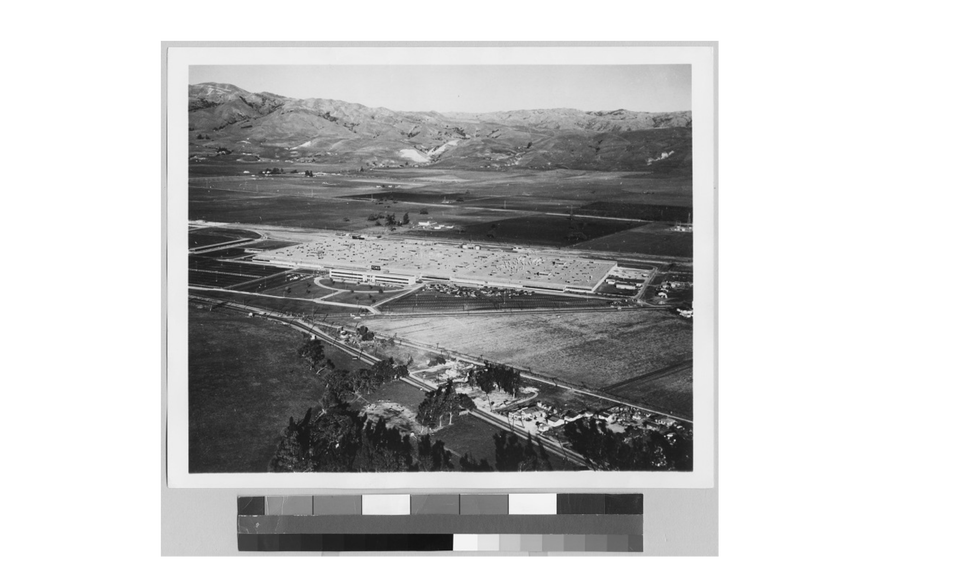
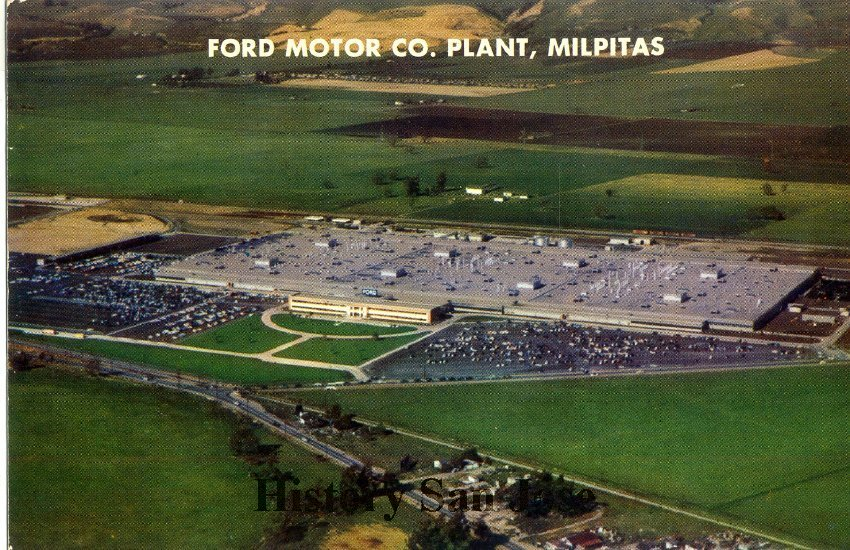
Ford Motor Company. This photo is before the Milpitas Plant, talk about County living.
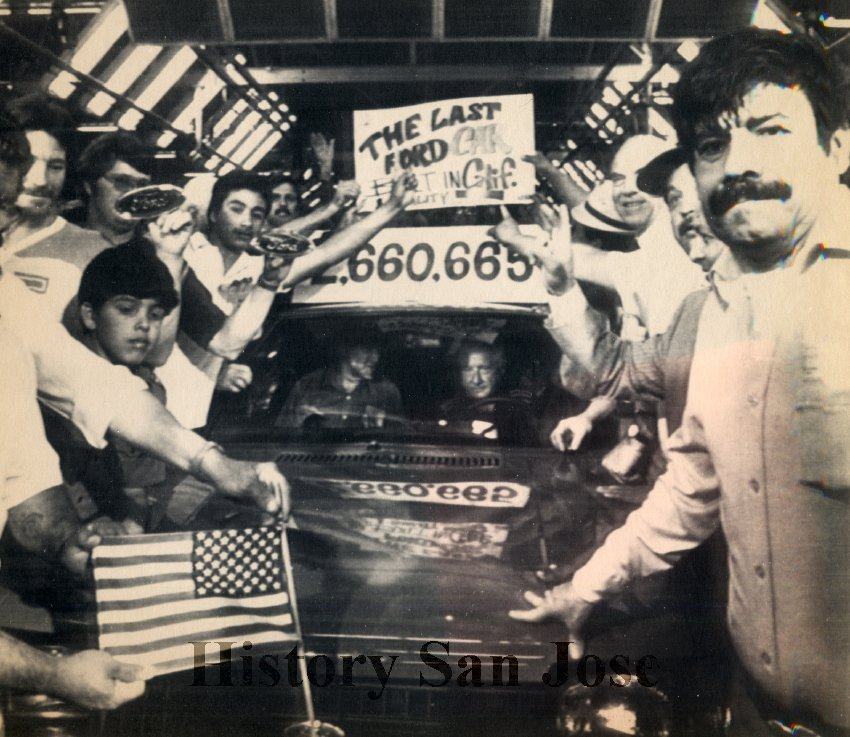
Here's a letter I wrote to the then, Mercury News.
Ms. Jennifer Bjorhus
San Jose Mercury News
750 Ridder Park Drive
San Jose, CA 95190
Dear Ms. Bjorhus,
On June 5, 2002 you wrote an article on Waukesha Electric Systems. Though the plant has been under different ownership in the past, the plant has been in Milpitas for more than 35 years. I work at this plant and have been here for 33 years. This particular plant builds high power transformers. As a group, we feel that SPX has been given the wrong numbers for our plant with the intention of keeping the other two sites open. Through confidential sources we have received new information that our CEO has made a great mistake now in shutting us down. Additionally, she has recently made the comment that she has underestimated the Milpitas site. At this time, we don’t know if SPX, (our parent company), can rescind their decision to close the plant.
You’re probably not familiar with our plant or transformers in general so let me explain. The three-sizes we build are, 50, 70, and 90 thousand series. The 90 thousand series is the biggest and the moneymaker for the company. These units go into substations or dams. All of these units are custom built by us according to our customer's design. Because of the size of the 90 thousand series, they can only be built at the Milpitas site. In fact, we are the only transformer company in the USA that can build the 90 thousand series transformers. The Milpitas plant can also build the 50 and 70 thousand series and have been for years. However, the other two plant sites that Waukesha Electric owns can only build the smaller units. Waukesha plant builds the 70 thousand series and the Goldsboro plant builds the 50 thousand series. We are the only transformer manufacturer left in the United States.
It has taken us 10 years to design and preen the 90 thousand series units, which are being improved on a daily basis. Yet, the company believes the Waukesha plant can do it in a couple of years, this will be very hard to accomplish if not impossible within this time frame. The employees at the Milpitas plant are a special breed. We have engineers that have published books on transformer theory. Also, everyone in the shop, at one time or another, has come across a problem in structural design and redesigned the problem themselves with approval from the engineers. The talent goes on and on. It is a dreadful shame to see it die with this plant closure. And we may never get it back. If we have an energy shortage, who will build the transformers to cure it?
From my understanding, we are the only site that is making money. In fact, it is said that we are covering for the other two sites so they can make their numbers to show SPX that they are making money, to avoid closure them -selves. However, they are testing units and they are failing one after another and not meeting specs. Consequently, they pencil whip the paper work so they can ship out units to make their numbers. It’s a strong possibility that the customers do not even know this is occurring.
So, if we are the only plant out of the three plants making money, why are we being shut down? We have written to everyone on this issue. It seems the only one left is the Pope!
We wanted to inform you of our side of the story and hopefully you will find this letter important enough to do a follow-up article or carry out a further investigation....
We prefer to remain anonymous and not leave our names, however we are available after 2:30 Monday – Friday on Piper Drive. Thank you for your time.
Sincerely,
Waukesha Electric Associates
Here is another letter I wrote to the CEO of SPX on behalf of the employees.
Sunday, March 20, 2022
cc: Patrick J. O'Leary
Robert B. Foreman
Christopher J. Kearney
Charles Bowman
Dear Mr. John B. Blystone and Board Members,
We are associates of Waukesha Electric Systems and we work in Milpitas California. We are also stockholders in SPX Corporation.
We build high power transformers in Milpitas for our customers. Many of these transformers are custom built units to our customers’ specifications. Our customers rely on us to produce quality units for them; and we do. We build units for our customers, which do not fail! Our customers rely on us and have for many years because we build quality units.
Even though Nancy Dickman made an error in her figures about us, more importantly, she admits she underestimated the Milpitas plant. We can honestly say we knew Ms. Dickman was wrong about her decision and the truth became apparent in the end. However, it is not over yet.
Winders from the Waukesha plant are arriving in Milpitas soon to “learn” how to wind the type of coils we wind. There is no time now to learn something that took us 10 years to perfect and furthermore they do not understand the technology…all this because they are closing us down. Why would anyone want to build our high-power transformers that do not have the technology and knowledge of winding these coils?
The BOTTOM LINE will show the staggering results about us! We are more then capable and reliable; we know what we are doing even with the knowledge of our plant closure looming over our heads. With our management team currently operating our plant can you imagine what we are capable of doing if we remain open?
THE BOTTOM LINE: We are the ones making the money!
Sales for September 2002
Operating Profit
Operating Profit Percent
$11.2M
$ 1.93M
17.2%
Investigate and Ask the Correct Questions and Question ALL Answers You Receive…
Thank you for your prompt attention to this matter.
Sincerely,
The Associates of WES, Milpitas California
Don,
Can't thank you enough for sharing with me the NAT newsletters and reading about how folks are doing since Waukesha made the decision to close the plant. Wanted to bring anyone interested, up to speed, on my life since then. I think some people may be under the impression that some of us were treated differently. Nothing could be farther from the truth. Here's the Lloyd Koehler story. Please feel free to share it with all.
In early January, following the plant closure at year end, I was informed by Waukesha that I had to return the monies given to us to relocate to CA from NC. That involved the purchase of our home in Pleasanton, so we had to sell the house and turn over the proceeds to Waukesha. As you can imagine that put a tremendous strain on our marriage and eventually, I returned to Florida to look for work there, while Linda remained in CA. After unsuccessfully looking for work in FL, I returned to CA, moving into a house Linda had rented following the closing of the Pleasanton house. Must have applied for several hundred jobs as the collapse of the Silicon Valley high tech industry had put so many people out of work that HR folks were a dime a dozen. After more than a year of being out of work and unemployment exhausted, I had an opportunity for a job with a hospital in Conrad, MT (rural North Central Montana) making about one third the pay I was making previously. Moved to Montana in early 2004. Shortly thereafter, my son Scott, who had just completed his MBA Degree in Washington state, moved in with me and took a job also at the hospital, Pondera Medical Center. Scott met a local gal with three children from a prior marriage, they got married and a year after started their own family, with a beautiful little girl, Kyleigh. In the interim, Linda and I finalized our divorce, and I met a wonderful Montana rancher, Ruth Livingston. Ruth will become Mrs. Koehler right after the new year.
Found myself commuting almost 4 hours each weekend to travel to Garrison, Montana near Deer Lodge. Linda owns a beautiful 5-bedroom (4500 sq. ft.) log home overlooking the Little Blackfoot River. Montana is a wonderful place full of very down to earth people. The locals refer to it as "The Last Best Great Place". While at Pondera Medical Center, I finished up requirements for both a Master's Degree and PhD in Industrial and Organizational Psychology. In October of 2005, I received a call, out of the blue, from a friend in NC who is a psychologist. Wanted to know if I was at all interested in returning to NC as she was working with a company that was looking for someone with a background like mine. In January 2006 I started as Sr. Human Resources Manager for one of the largest non-woven manufacturing plants in NC, Polymer Group, Inc. Reminds me a lot of the Milpitas plant. Similar long term, hardworking, good, down to earth people. Ruth and I will be returning to our Montana home in March 2008 and set up enjoying the life most Montanans love. In March of last year my dad, Lloyd F Koehler, died at the age of 96. I'm so thankful, I had the opportunity to be back in this area and close enough to spend time with him during those last precious years.
Like everyone who worked at Milpitas, the plant closure greatly affected my life. Negatively at first but eventually brought a lot of growth and a better life than I had before. The 18 months without a job were extremely difficult but sure gave me a chance to sort out what is really important in life. It really is what you make of life and the friends along the way that are always there. For those interested, our home in Montana will always be open for your visits and I'd love to show you the Last Great Best Place. Take care. Interim contact information:
Lloyd K. Koehler
717 Carolina Drive
Dunn, NC 28334
(910)980-3232 home
(919)207-3232 work
(406)450-0604 cell